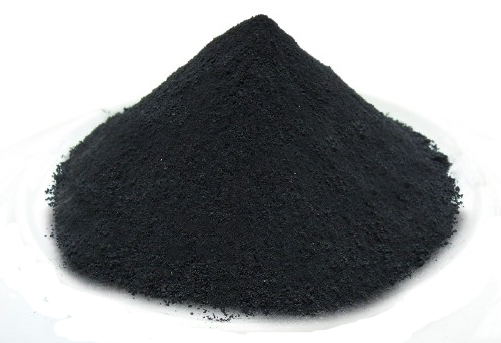
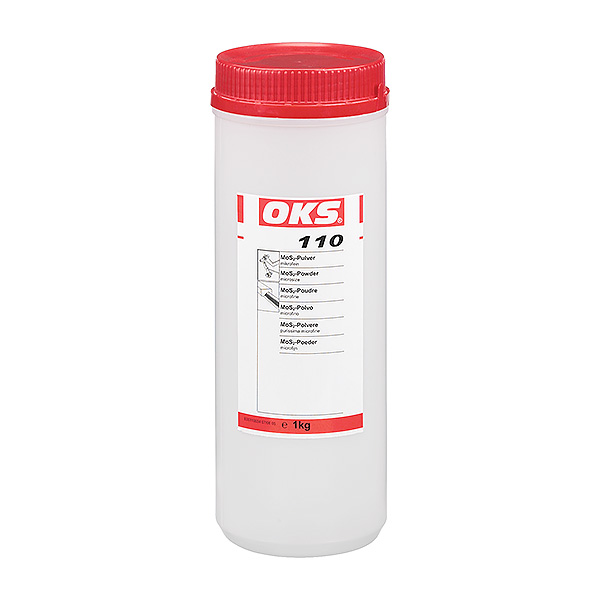
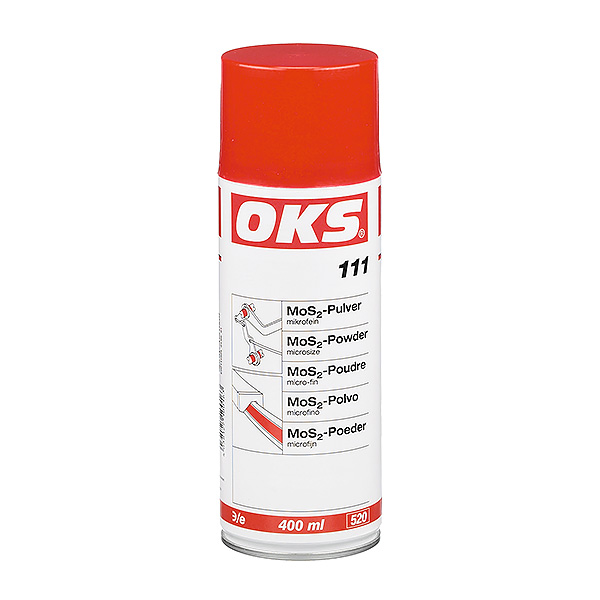
Vamos a seleccionar este producto entre varios sólidos inorgánicos con estructura laminar para desarrollar sobre sus propiedades que lo hacen único y especial en el campo de la tribología. El grafito es conocido desde el siglo XIX fue usado como lubricante para forjado de metales con regular adhesión y problemas de carburación de herramientas en el moldeo en caliente. Su capacidad lubricante se correlaciona con su estructura molecular con fuertes enlaces carbono-carbono en cada capa y débil enlace entre capas. Como lubricante sin embargo presento elevado rozamiento y desgaste. Es muy estable térmicamente y no es afectado por la radiación. Por sobre los 450ºC con acceso de aire se transforma en CO2 gaseoso de modo que no presenta fenómenos de abrasión. El disulfuro de molibdeno se conoce hace unos 300 años cuando era utilizado por los artesanos en prensas y herramientas. Fue ampliamente usado durante la segunda guerra mundial para reducir fricción y desgaste en la maquinaria bélica.
Luego de un procesos de purificación se obteniéne un grado con especificación estricta en diferentes granulometrías siendo su formula.
El MoS2 tiene aspecto similar al grafito pero su densidad es más del doble: 4,8g/cm3. No es conductor y es diamagnético. Es inocuo, no ataca la piel, es insoluble en agua fría o caliente y resiste ácidos excepto nítrico, agua regia, flúor y cloro. Es térmicamente estable entre -180ºC y +450ºC; +630ºC sin acceso de aire y +1340ºC en atmosfera de argón. Presenta una estructura laminar de tres capas, una central de Mo y dos laterales de S que actúan como una fuerte unión iónica, resistiendo así la rugosidad de las superficies. Las láminas de disulfuro son tan delgadas que 1600 de ellas presentan un espesor de un micrón, y su resistencia a la presión supera el límite de fluencia de los metales conocidos (30.000Kg/cm2).
El coeficiente de rozamiento disminuye con cargas crecientes. Su efecto lubricante se explica por la fuerte adhesión de los átomos de azufre a las superficies metálicas y la facilidad de deslizamiento de las laminillas. La propiedad del disulfuro de adherirse a las superficies metálicas por los desplazamientos debido a la exigencia mecánica es su mayor diferencia respecto de otros lubricantes sólidos y explica a su vez la reducción del coeficiente de rozamiento.
La oxidación en presencia de oxígeno comienza en forma notable al superarse los 400ºC obteniéndose trióxido de Molibdeno el cual actúa como protector de las capas inferiores de la película lubricante que permanece inalterable.
El asentamiento es la fase inicial de la puesta en marcha de un motor de combustión interna. No se ha podido determinar exactamente cuando se cumple dicho periodo de reducción a un mínimo de la abrasión, consumo de aceite y combustible, es decir máximo rendimiento del motor. Durante el periodo de asentamiento se producen soldaduras, engranes, y desgaste por el contacto metálico directo. La forma más efectiva para reducir el coeficiente de rozamiento, la abrasión y los daños originados durante el asentamiento es la utilización de purísimo disulfuro de molibdeno. Cuando el lubricante sólido cubre el área de contacto real, no puede producirse la soldadura en frío y las crestas de la rugosidad superficial son deformadas plásticamente.
La dispersión de disulfuro de molibdeno OKS agregado al aceite de motor da una mejor calidad de las superficies portantes y un aumento del rendimiento, mayor vida útil y mejores condiciones de servicio. Simultáneamente tratando los componentes mecánicos expuestos a rozamiento con la pasta OKS 200 al armar el motor se obtiene un aumento de potencia y una disminución de la temperatura de los gases de escape sin importar que los aros de pistón sean o no cromados, el tipo de motor ni el aceite lubricante usado.
El agregado de la dispersión de disulfuro de molibdeno OKS a un aceite para motor de combustión interna forma, durante su funcionamiento, una película deslizante sólida que protege contra el desgaste y disminuye el coeficiente de rozamiento ,dando así, una lubricación de emergencia, y evidenciando un aumento del rendimiento, economizando combustible y lubricante, facilita la puesta en marcha y se observa un funcionamiento más suave.
Protege cilindros, aros, cojinetes, árbol de levas, guías y vástagos de válvulas. Facilita el desplazamiento de los aros en las ranuras de los pistones y hermetiza el cárter contra la fuga de los gases de combustión.
Este aditivo no sedimenta ni provoca obstrucción en los filtros, mejora la lubricación y aumenta la eficiencia de los aceites.
En las últimas décadas las condiciones de servicio de los ejes traseros han incrementado su severidad. El diámetro de la corona del diferencial se ha ido reduciendo mientras la potencia y el numero de revoluciones se ha más que duplicado.
Los engranajes de automotores se han sobrecargado y por lo tanto se ha dificultado su lubricación. Más y más se han combinado la fricción rodante y deslizante dando lugar a engranajes hipoidales y sinfín y a mayores exigencias de impacto contribuyendo a una mayor exigencia en el diseño del lubricante. La carga y la velocidad provocan un mayor rozamiento en el diferencial y por consiguiente mayor temperatura que puede superar los 150ºC y aún 180ºC. La temperatura destruye los aditivos químicos EP y por lo tanto los retenes y el piñón. Se probo entonces el agregado de la dispersión concentrada de disulfuro de molibdeno OKS 300 lográndose una disminución importante de la temperatura (48ºC),a la vez que disminuye el ruido un 30%, obteniendo un perfecto estado de piñón y corona.
Iguales resultados se han logrado en las cajas de cambio sincronizadas sin afectar en absoluto su funcionamiento.
Se ha comprobado la disminución dramática del desgaste en las partes del chasis lubricadas con OKS 400 lo que condujo a la investigación de la disminución de la frecuencia de lubricación y por lo tanto del mantenimiento por la lubricación larga vida incorporando polvo de disulfuro de molibdeno (OKS 110) a componentes de hierro sinterizado.
En la tracción delantera las bolas y las pistas de las juntas homocinéticas son tratadas con la laca OKS 511 antes del montaje, y luego se lubrica el conjunto y las uniones universales con OKS 400.